Maîtriser les coûts
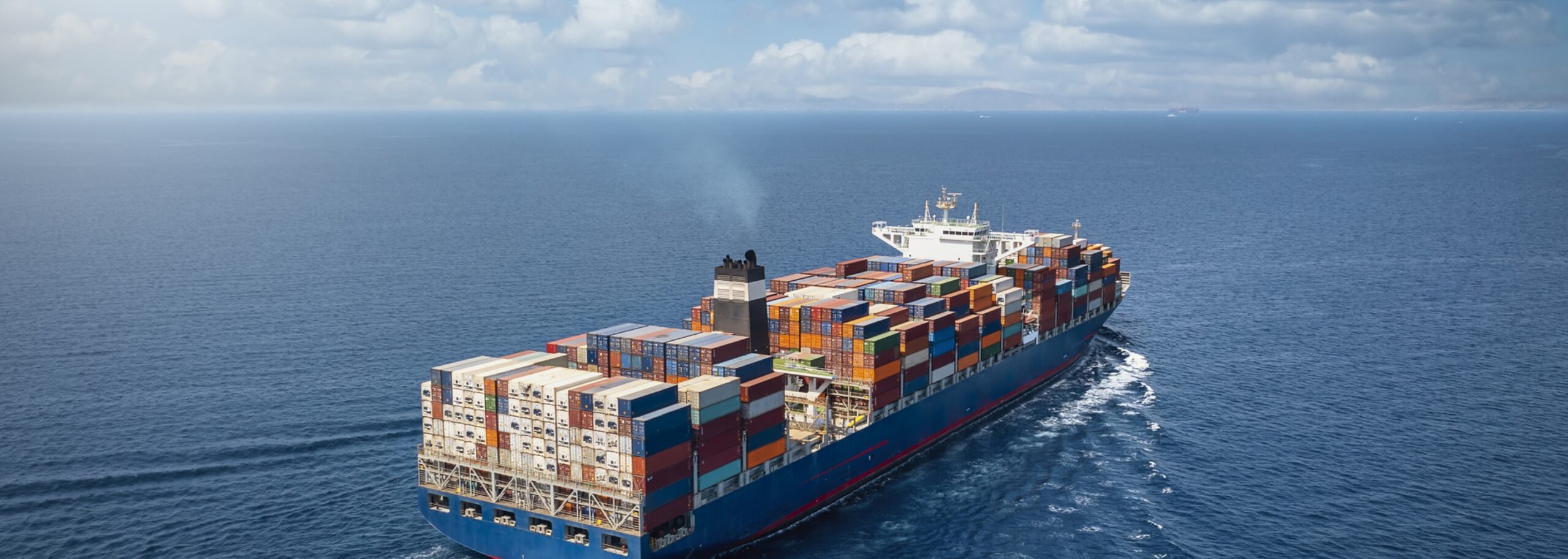
L’entreprise
Un grand armateur opérant une flotte de plus de 250 navires. Une direction industrielle assure la modernisation et la maintenance de chaque navire dans des chantiers navals situés dans le monde entier.
Le contexte et le problème posé
La flotte est en forte croissance depuis plusieurs années. Les navires sont par ailleurs soumis à des contraintes environnementales qui imposent des évolutions technologiques à intégrer aux arrêts techniques pour maintenance. Une foison de défis techniques et organisationnels étaient à résoudre.
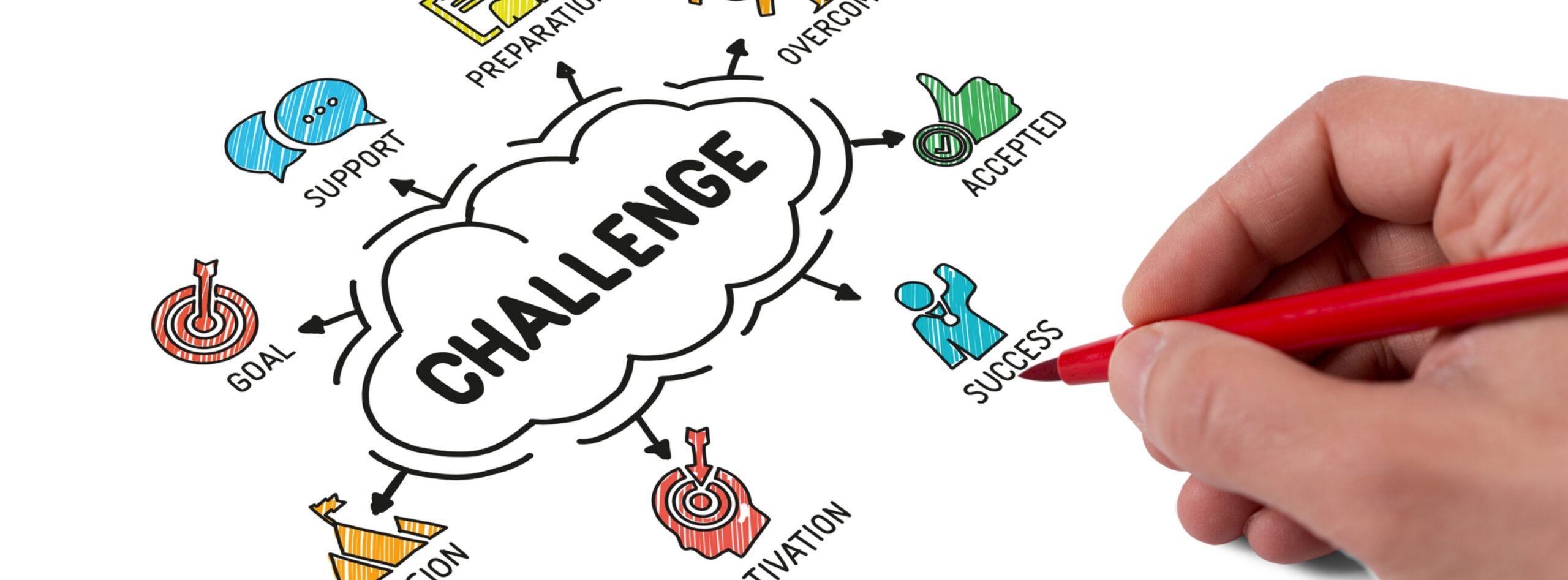
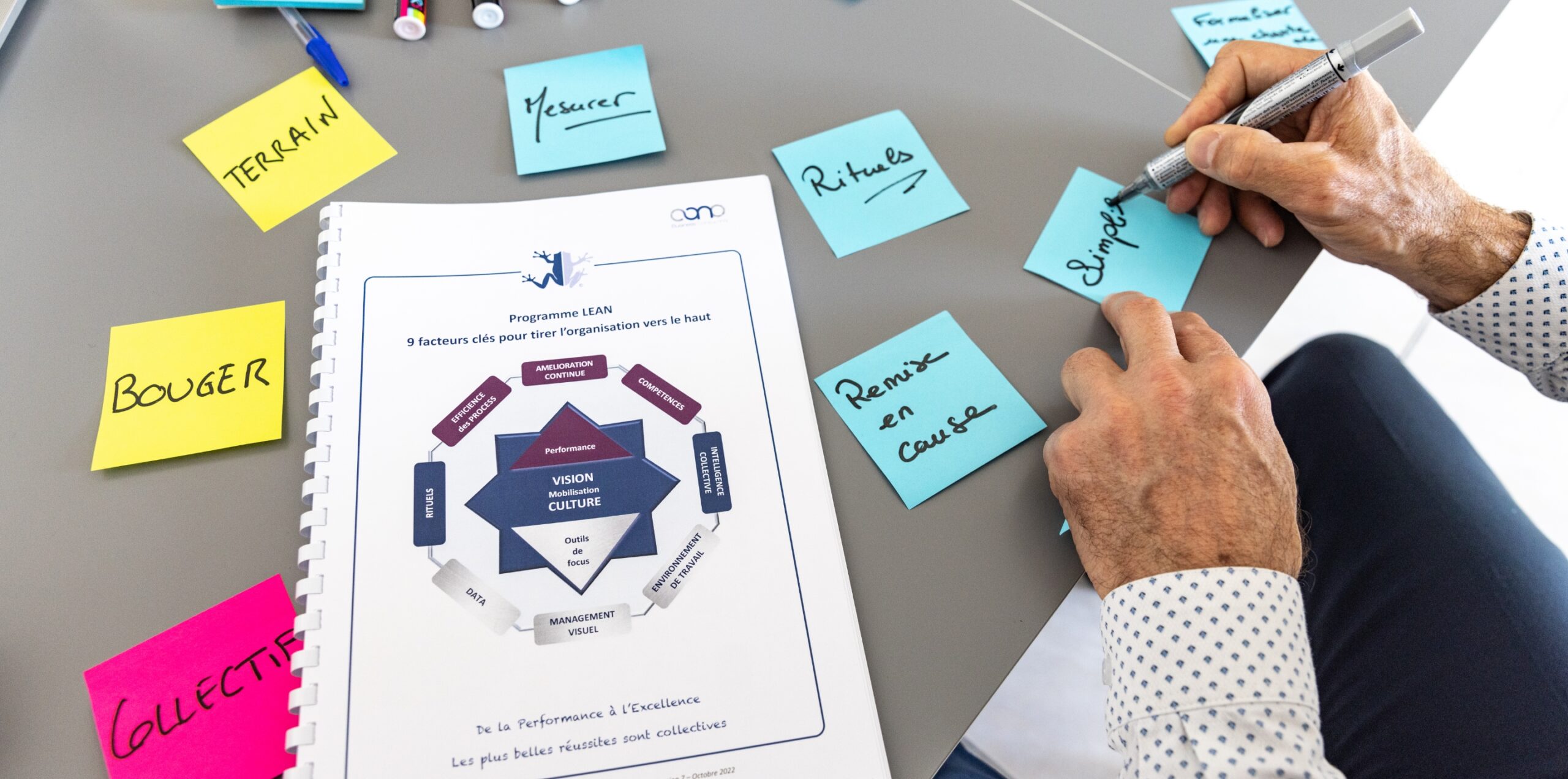
L’approche retenue
Dans un premier temps, l’équipe de direction a bénéficié d’une formation à la culture et aux outils du lean management. 9 facteurs clés de succès ont été transmis et appropriés durant les 6 mois du programme « Accélération de la Transformation vers l’Excellence ». Individuellement et en équipe les directeurs ont été invités à prendre du recul et à remettre en cause certaines de leurs pratiques managériales. Ils ont ainsi clarifié leur stratégie de transformation, élaboré une feuille de route du progrès, revu le rythme, l’animation et la qualité de leurs rituels d’équipe. Ils ont par ailleurs intégré les outils du lean dans leurs pratiques managériales, depuis l’Hoshin Kanrin jusqu’à la maîtrise des non Valeurs Ajoutées en passant par les démarches structurantes comme les chantiers DMAIC.
Dans un second temps, un projet d’amélioration de la préparation des arrêts techniques a fait l’objet d’un accompagnement spécifique. Le process général a été revu, de nouveaux outils de pilotage ont été mis en place, les compétences et les ressources ont été rééquilibrées afin de gagner en fluidité et en prédictibilité des coûts.
Les bénéfices
La première phase a permis de renforcer la confiance et la co-responsabilité au sein du comité de direction. Les rituels, plus dynamiques et efficients, ont largement contribué à resserrer les rangs et à renforcer l’esprit d’équipe.
L’Hoshin Kanri a clarifié et cadencé les chantiers de progrès qui étaient trop foisonnants. Les équipes se sont trouvé plus mobilisées sur des objectifs stimulants. Le chantier portant sur la préparation des arrêts techniques a renforcé la collaboration avec les parties prenantes de ces opérations. Les jalons de préparation ont été clarifiés, cadencés et respectés. Des outils de pilotage des coûts ont permis de mieux identifier les gaspillages et de fiabiliser les prévisions budgétaires. En 6 mois, une économie de 5% a été réalisée, soit environ 50 fois l’investissement lié au projet.
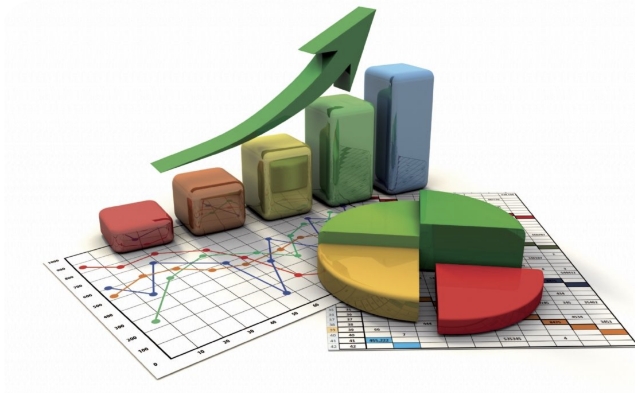